- Sponsor:
- STELIA Aerospace
- Industry Mentor:
- Emeric Noirot-Nérin
- Faculty Adviser:
- Dr. Santosh Devasia
- Team:
-
- Chayanat (Luke) Wanitthananon
- Drew Byungkyu Kang
- Daniel Varnum-Lowry
- Taehan Kook
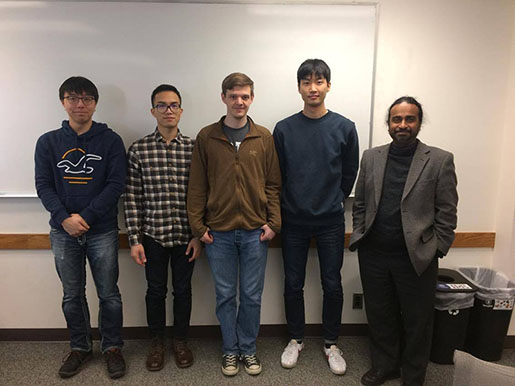
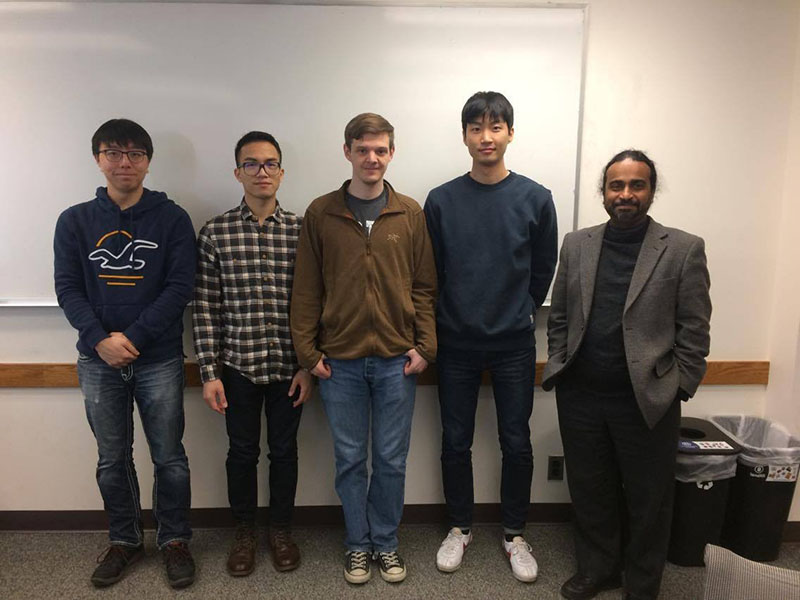
The STELIA team. From left to right: Drew Kang, Eulong (Luke) Wanitthananon, Daniel Varnum-Lowry, Taehan Kook, and Dr. Santosh Devasia

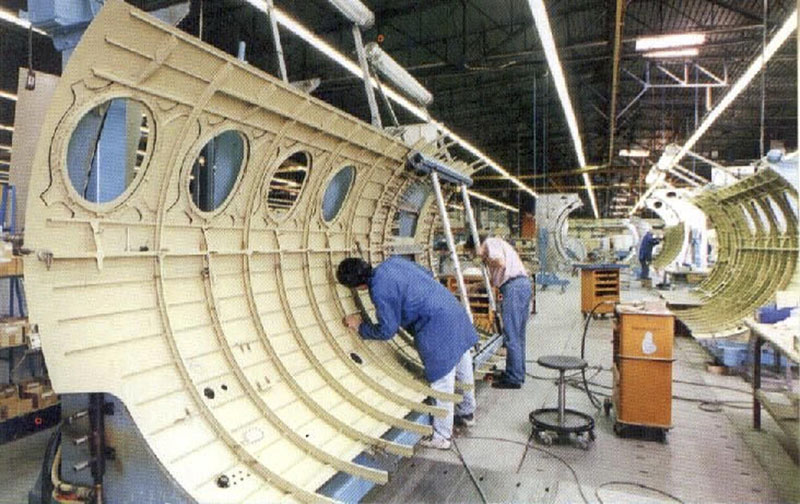
The current solution for bracket installation method – mostly manual w/ some robotic assistance through laser sensor. Our goal is to fully automate this procedure!

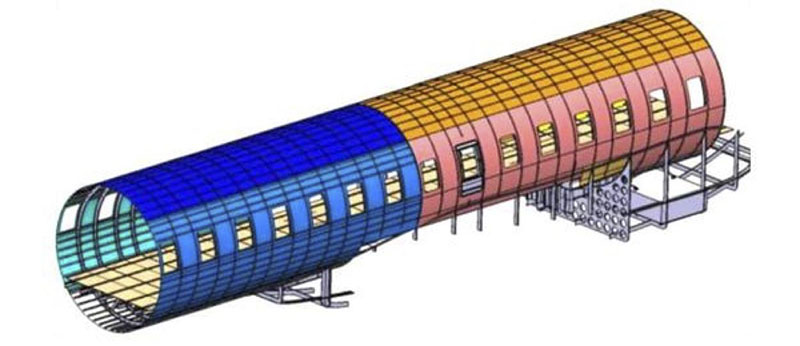
Brackets will be installed on Stelia aircraft fuselages. A very tight tolerance to respect and hard to access location would require creative approach to Human Robot interaction!

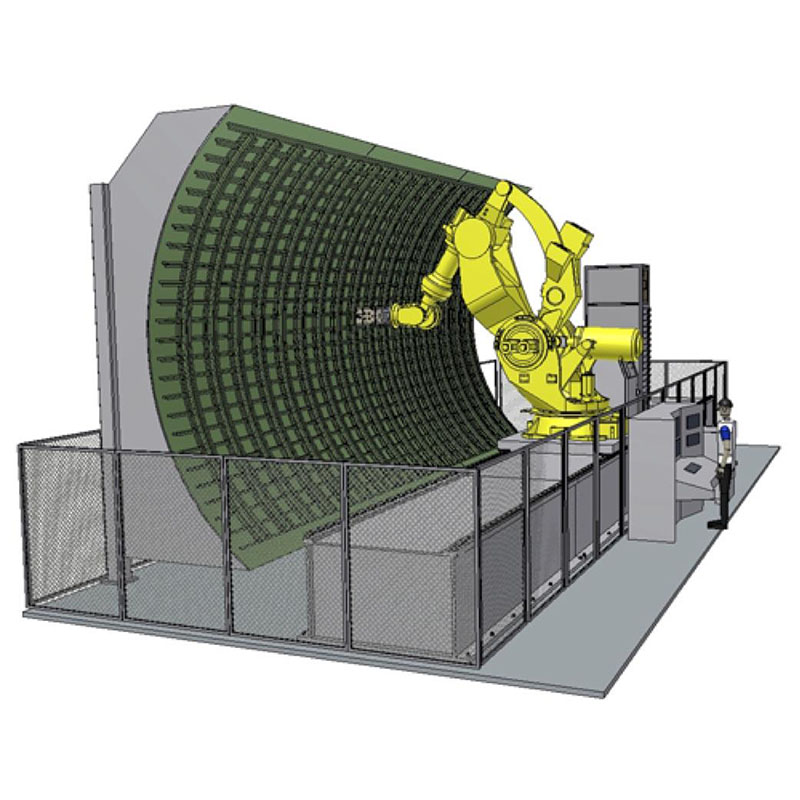
Our plan is to develop a simulation that will serve as a framework for the robotic solution for bracket installing assembly robot!

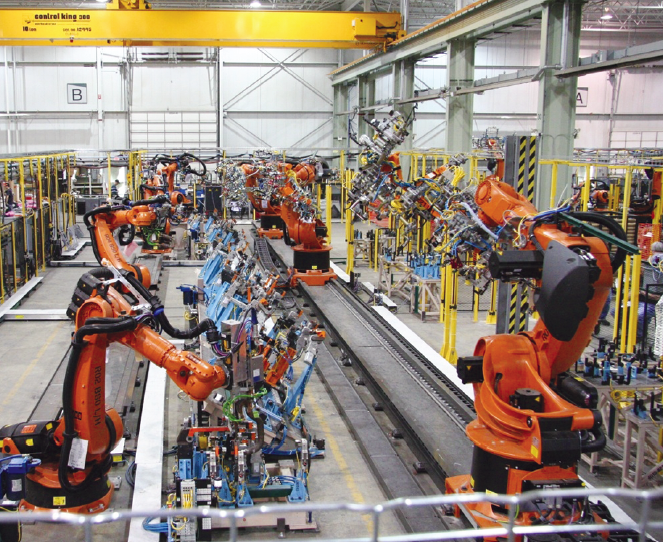
To determine the basic requirements and expectation of our solution, we will explore several of KUKA’s assembly robot models. These robots will also help us better understand the manufacturing process in today’s industry.

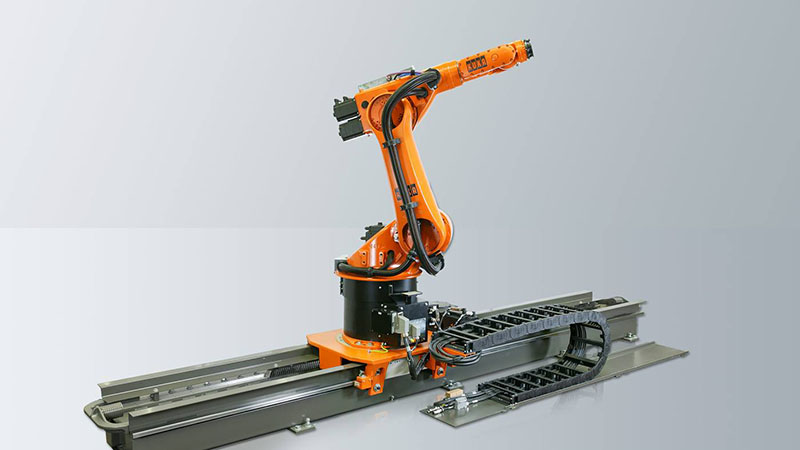
For the mobility of the assembly robots, there are two possible apparatus that we can use: the drive platform, or the rail system. We will explore both of these methods to determine which one suits our needs most.

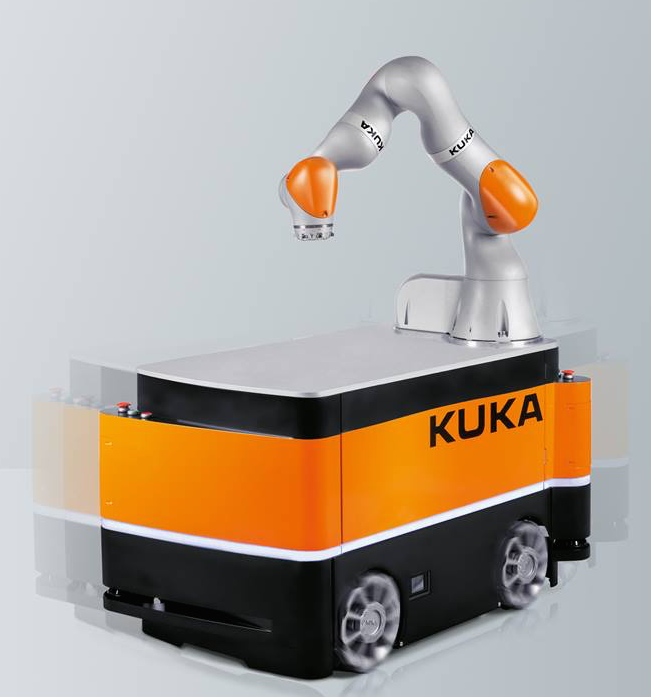
For the mobility of the assembly robots, there are two possible apparatus that we can use: the drive platform, or the rail system. We will explore both of these methods to determine which one suits our needs most.

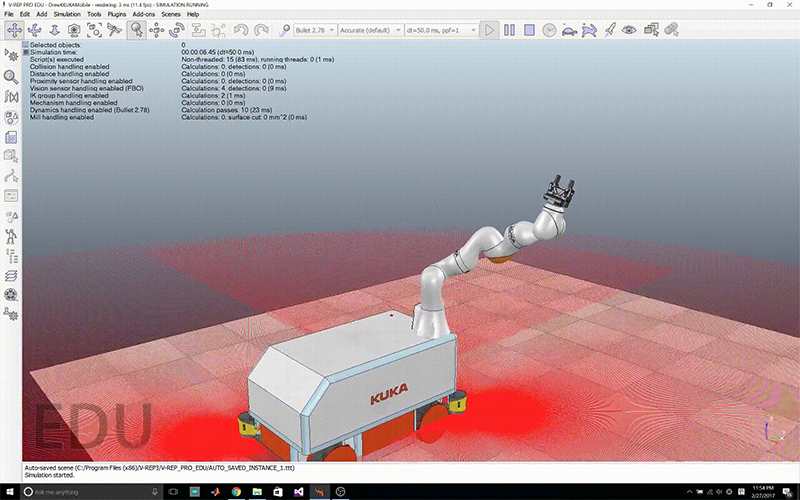
Another useful robot simulator will be explored (V-REP), to demonstrate the possible solution for our bracket installing procedures.
The purpose of this project is to investigate and improve STELIA Aerospace’s current bracket installation apparatus and procedure. Brackets are non-supporting parts on aircraft used for guiding other non-structural components such as electronic wires through the fuselage. The current method employed by STELIA is mostly manual, and it involves using a removable bracket positioning tools, assisted by laser sensors to achieve the required tolerance. The company would now want to automate this procedure, using robotic solution to improve the installation time, accuracy, and reduce the cost of the operation.
Industry Mentor:
Emeric Noirot-Nérin
Emeric Noirot-Nérin is an engineer with 3 years of experience committed to innovation projects in maturing technologies for Aerospace Industry. His professional experience lies in non destructive composite testing, engineering methods & tools development for structure optimization, manufacturing capabilities optimization . He is currently in charge of North American Research & Technology at STELIA Aerospace.
STELIA Aerospace
STELIA Aerospace is an aerostructure design and manufacturing company, that also designs pilot seats and premium class passenger seats for aircrafts and airlines. The company was merged from two Airbus Group business units (Aerolia and Sogerma), on January 1st, 2015.